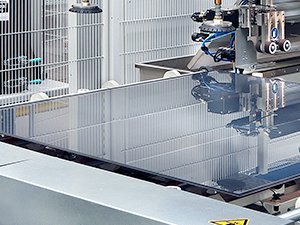
Solar Module
Assembly
BENTELER offers various solutions for the module assembly.
Solar Module Assembly
Manufacturers of solar and photovoltaic modules around the world rely on BENTELER Glass Processing Equipment's systems. For module assembly, we develop innovative solutions characterized by modular design, high automation levels, and great process reliability. This enables our customers to achieve optimal flexibility, reliability, and short cycle times.
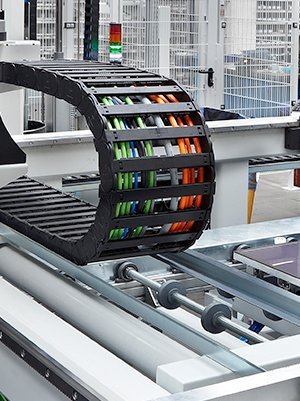
With extremely high precision, the BENTELER Edge Sealing System creates a seam made of butyl hotmelt. Depending on the preferred EVA or PVB laminating foil, the sealing seam is exactly formed and laid down on the solar module. The machine design places maximum value on process reliability. Laser-based sensors permanently monitor the sealing seam. A massive centering table ensures the necessary firm hold of the glass for uniform quality. The robust design and the simple operation permit global use.
Advantages
Use of more cost efficiency laminating foil:
- Increase in competitiveness
Improved protection of the module against moisture:
- Longer product warranties possible
Extremely high working speed:
- Improvement of the cycle time
MES linkage:
- Simple integration into modern control systems
Maximum process reliability:
- Less faulty parts, less warranty cases
Modular design:
- Easy integration in existing production lines
Fields of application |
---|
Technical Glass |
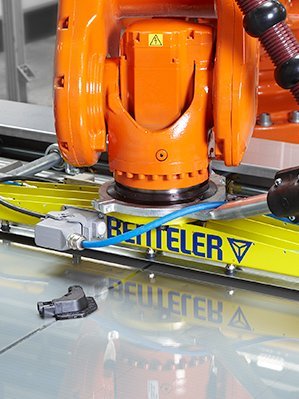
BENTELER offers various plant conceptions for so-called "railbonding". No matter whether a simple "tape“ based adhesive technology is desired, or a 1K or 2K adhesive or a combination of tape and adhesives is required, BENTELER has an appropriate solution for its customers. We combine these with practically every kind of available rails. Our portfolio also includes integrated equipment for pretreatment of the rails by means of cleaner and primer. The end result is that the customer receives a modularly designed, individual machine for 24/7 continuous operation according to the requirements of modern solar module production.
Advantages
Completion of the "solar module product" with an appropriate assembly system
- Added value for the final customer
- Reduction of glass break risk due to stress and fatigue
Practically any process combination rail/adhesives/glass is possible
- Individualization according to customer wishes
MES linkage:
- Simple integration into a modern control system
Process reliability:
- Less faulty parts, less warranty cases
Modular design:
- Simple integration in existing production lines
Fields of application |
---|
Technical Glass |
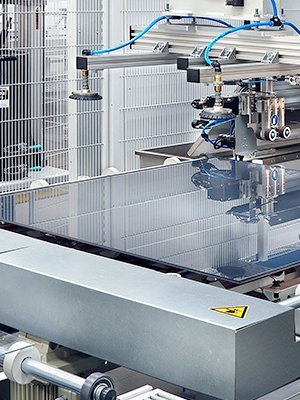
The BENTELER Foil Management stands out for its extremely high repeatability for cutting and positioning foil as well as extremely high availability. The machine is individually adapted to the characteristics of the respective foil.
Advantages High availability:
- Mature design as a result of decades of experience in laminated glass production
- Automatic roll change and foil start
- Automatic wind-up device for interleave foil
High precision:
- Automatic laser measurement of the foil leading edge
- Edge guidance to compensate for wrapping deviations within the foil rolls (option)
- Exact synchronization of the work table and laying roller
Great flexibility and high operator comfort:
- Siemens S7 control system
- MES linkage with BENTELER SECS/GEM interface
- Documentation and tracing of consumables
- Barcode reader for documenting and identifying of foil rolls
High cost efficiency:
- Lower waste by high positioning precision
- High cutting speed
- Integrated foil punching device for the bus bars
Fields of application |
---|
Technical Glass |