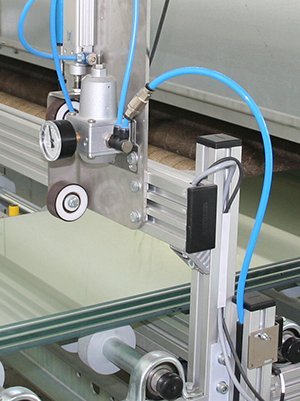
Laminating Lines
BENTELER offers many solutions for several different glass laminating needs due to four various machine options.
Laminating Lines
BENTELER Glass Processing Equipment supports efficient and cost-effective laminated glass production with innovative processing lines—worldwide! Energy-optimized and state-of-the-art: With our decades of experience, we provide the right solution for every requirement—from manual to fully automated lines and for all common types of interlayers such as PVB, EVA, or SentryGlass® (by DuPont).
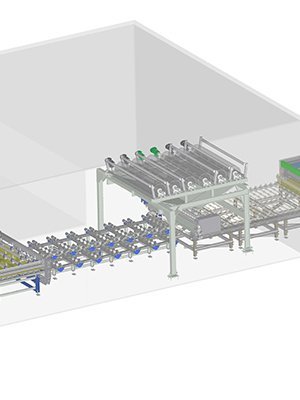
The Tec Lami Line is a standardized line with a high quality washing machine and the same oven technology as our custom size or jumbo laminating lines. This oven is able to handle all kinds of glasses and products, with a low energy consumption. The tecLami Line has all important components for the laminating process. An upgrade is possible at any time.
Advantages
High precision:
- accurate glass washing
Flexibility:
- for all kind of foils
Process reliability:
- with the BENTELER recipe control
Simple operation:
- easy operating instruction menu
Technical data | Fields of application |
---|---|
| Architectural Glass |
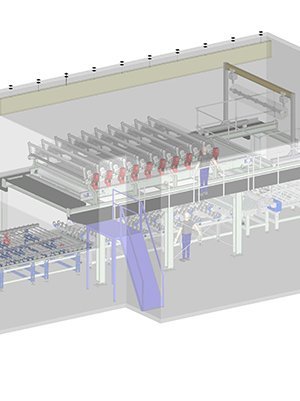
The Custom size laminating line is individually designed to the request of our customers. The PVB storage is installed in the first floor with the possibility to handle cooled and interlayer PVB films. The storage can be build from 6 up to 24 PVB rolls with a separate steel construction. This steel construction will be used as well for the isolating panels for the assembly and storage room.
Advantages
High precision:
- accurate glass assembly
Flexibility:
- with a lot of available PVB films; cooled and interlayer foils
Process reliability:
- in the pressing and pre-laminating
Simple operation:
- with PVB unwinding and back edge
- cutting unit
Technical data | Fields of application |
---|---|
| Architectural Glass |
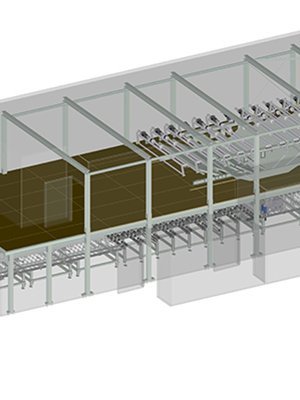
The Automatic Custom Size Laminating Line has the highest output on laminating products for PVB, EVA or SentryGlass*(by DuPont) of our lines. Due to the flexibility with the different programs, like automatic PVB laying and trimming or manual assembly with automatic trimming, the customer has always the possibility to use the optimal program to produce fast and cost efficient.
Advantages
High precision:
- accurate glass positioning
Flexibility:
- manual, semi- and full automatic processing
Process reliability:
- proven furnace technology
Simple operation:
- easy operation with Siemens touch panels
Technical data | Fields of application |
---|---|
| Architectural Glass |
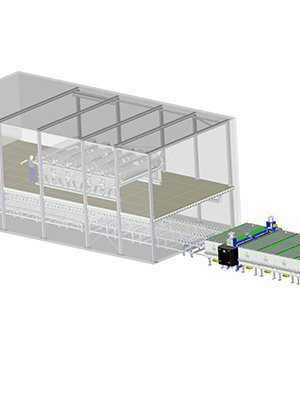
The Jumbo Size Laminating Line is equipped for fully automatic operations. The line provides optimal results within a cycle time of up to 45 seconds. All production steps are automated from the loading of coated glasses to the offloading with spacer setting. We also can provide solutions for the air conditioned clean rooms, the foil storage, as well for the autoclave and glass racks.
Advantages
High precision:
- automatic PVB laying and trimming
Flexibility:
- for jumbo and half jumbo sizes
Process reliability:
- in the assembly and PVB laying even for multiple layers
Simple operation:
- full automatic operation mode
Technical data | Fields of application |
---|---|
| Architectural Glass |
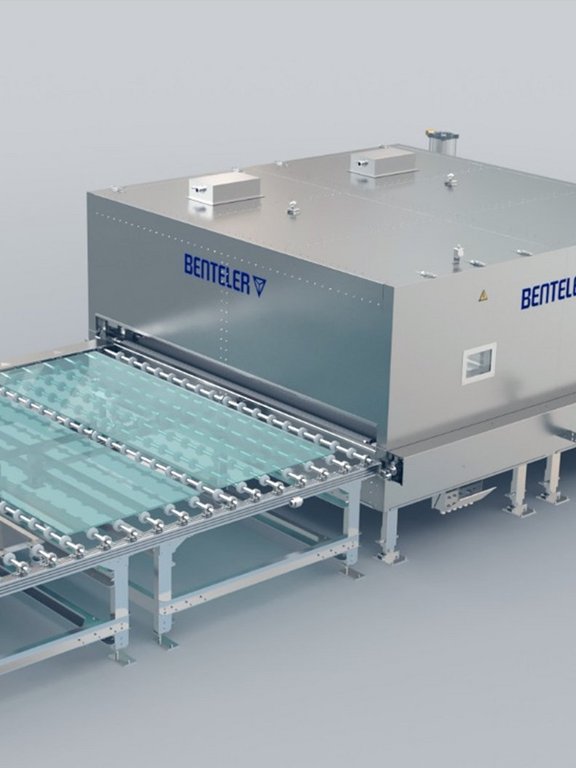
Intelligent production technology made by BENTELER! With the hybrid prelaminating furnace, BENTELER Glass Processing Equipment is breaking new ground in terms of energy efficiency: by optionally using two different laminating techniques for laminated glass in one plant, productivity can be increased while simultaneously reducing energy costs. Energy-saving, safe, fast: The hybrid prelaminating furnace combines two proven processes for laminating glass!
Advantages
High precision:
- Perfect laminating results
Flexibility:
- Different production types possible
Process reliability:
- Independent of glass type
Simple operation:
- Simple menu for operating instructions
Technical data | Fields of application |
---|---|
|
|
Did you know?
BENTELER Glass Processing Equipment successfully completed pre-installation of a new BENTELER tecLami Line in Dubai. With commissioning, pre-laminated glass will run off the line in the future. And that's not all: The BENTELER tecLami Line can be expanded with additional automatic functions. A solid basis for the development of an efficient and cost-effective laminated glass production.